Isogeometric Analysis & Form Finding
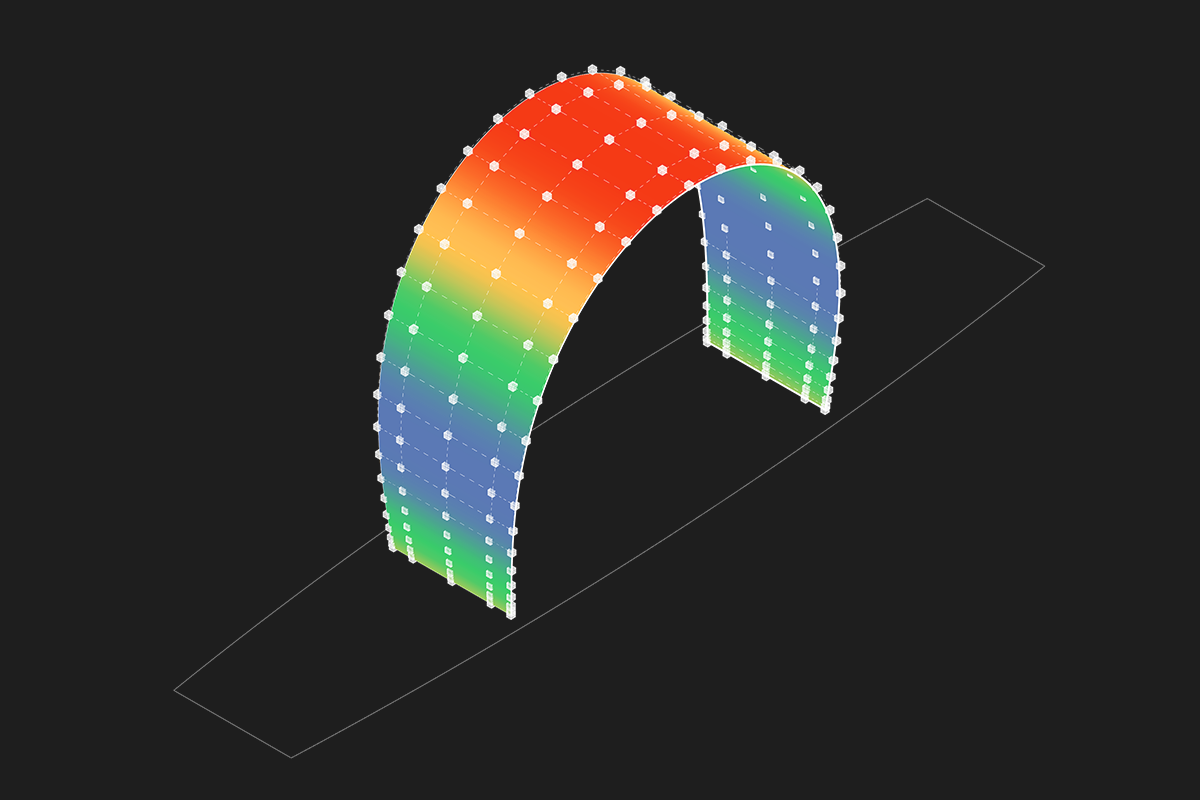
M.Sc thesis project
Academic
Tutor
Mats Ander, Jens Olsson
Examiner
Prof. Fredrik Larsson
Year
2018
External Links
Recent developments within the design of shells have seen an increased interest in utilizing active bending as form giving procedure. This enables complex structures to be built from simple off-the-shelf materials. However, forming bending-active structures is highly dependent on the material properties, which makes the design process reliant on either physical testing or digital simulations. An associated problem with the simulation of this behavior is the lack of integration between modeling and analysis in conventional simulation techniques, a crucial concern since the final design is always an equilibrium shape with requirements on both structural and spatial integrity. IsoGeometric Analysis (IGA) is a method that aims to bridge precisely that gap between analysis and design, making it a suitable method for bending active structural design. This thesis explores an approach to the modeling and digital design of actively bent shells using the implementation of nonlinear IGA.
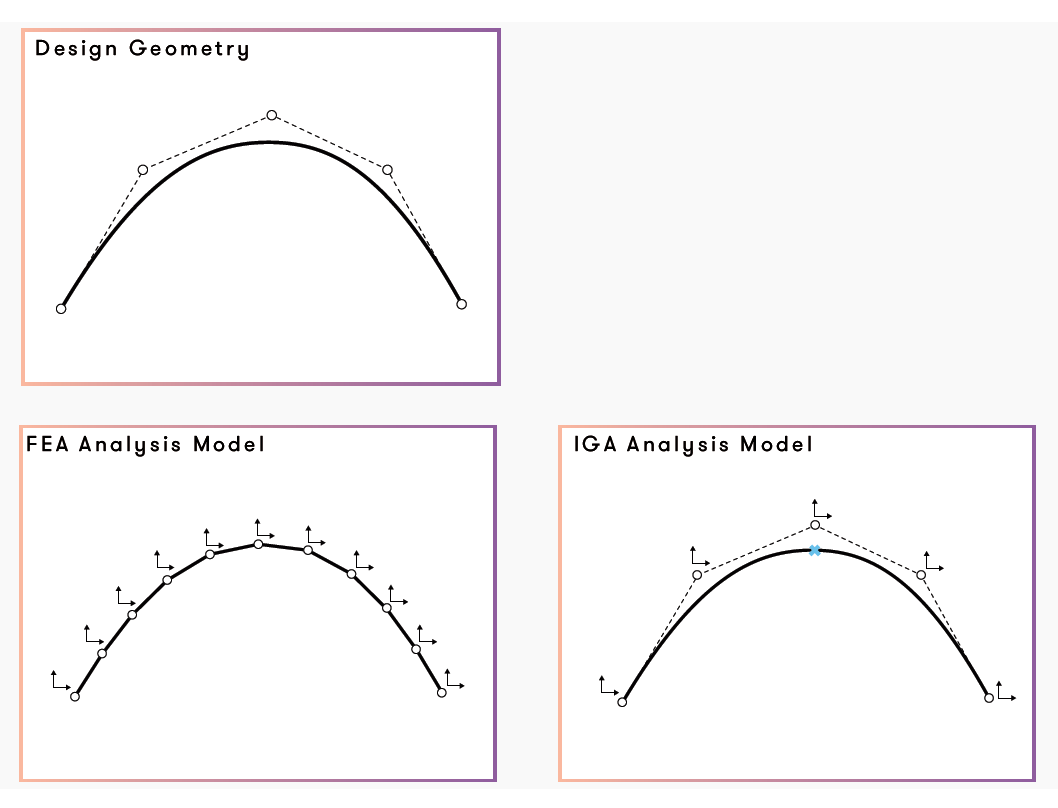
Isogeometric analysis is in many ways similar to regular FE analysis, with one major distinction. Instead of using a discrete geometric representation it uses the smooth, continuous basis functions of NURBS as basis for the mathematical formulations. This removes the need for meshing and the design geometry can be used for analysis. This is especially useful when dealing with actively bent shapes, as the design geometry will be a direct result of material properties, loads and an initial underformed geometry.

By being able to relate the deformed and undeformed states of NURBS geometries, these can then be correlated to a stiffness distribution, in this case thickness. The gif below shows a backwards process of finding a stiffness distribution which puts the circular shape in equilibirum with reference to a planar representation.
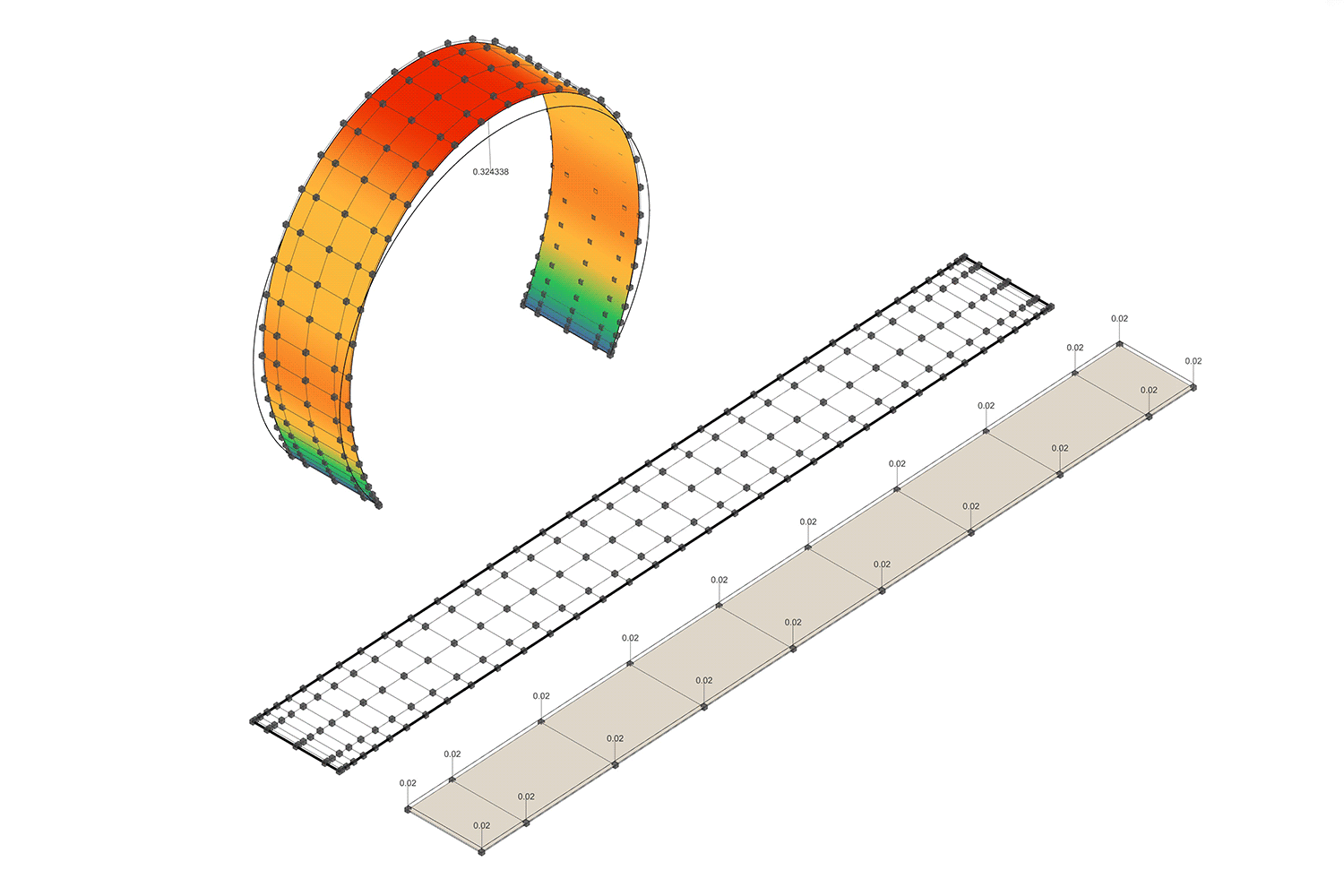
A process like this enables material programming which can be used to manufacture intelligent components, which need no construction information, as it's embedded in the material. The example below shows the form finding of bending a sheet into a specific shape as part of a temporary structure.
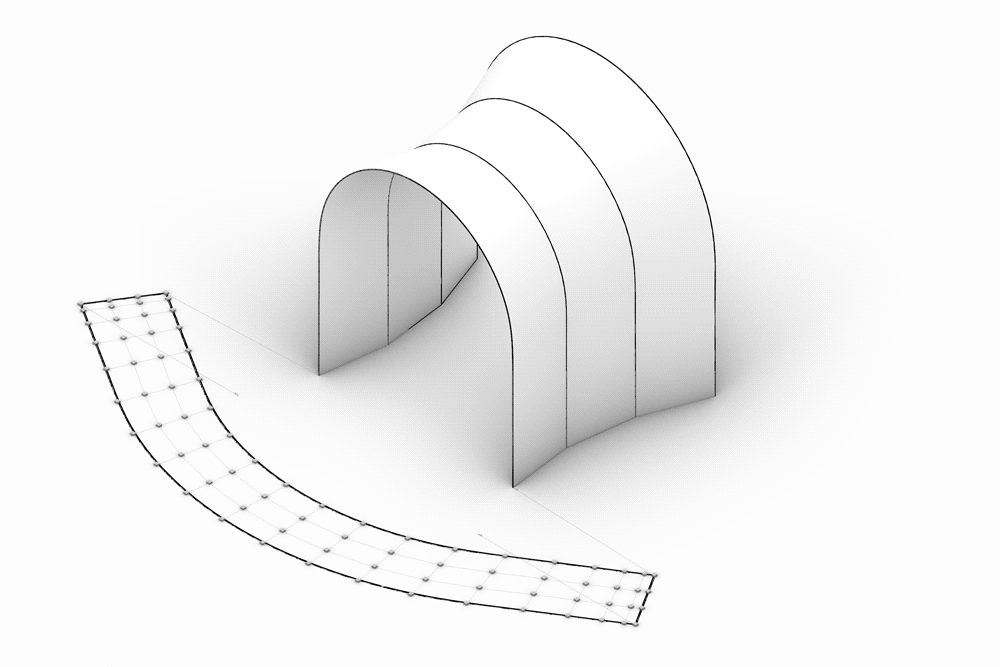